Profitable Digitalisierungsprojekte beginnen im Maschinennetzwerk
14.06.2022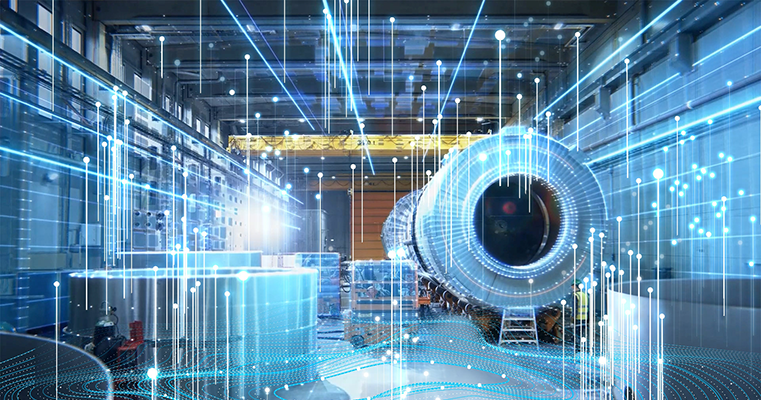
Fallbeispiele zur effektiven Datengenerierung aus dem Shopfloor
Wer Digitalisierungsprojekte auf Shopfloor-Ebene wie z.B. Energiemanagement, Condition-Monitoring oder vorbeugende Wartungskonzepte umsetzen will, kennt die Herausforderungen: Woher erhalte ich umfassende und passgenaue Daten? Wie kann ich die Kosten für infrastrukturelle Anpassungen auf einem angemessenen Niveau halten? Im Fokus liegen an erster Stelle die Steuerungen von Maschinen und Anlagen. Deren Netzwerke sind gewöhnlich in sich geschlossen aufgebaut, um Sicherheit und funktionale Zuverlässigkeit zu gewährleisten. Doch ließen sich die in der Maschine ohnehin vorhandenen Daten abgreifen, würde das Digitalisierungsprojekte erheblich vorantreiben. In diesem Zusammenhang kommt dem Netzwerk als Ganzes eine zentrale Rolle zu. Denn wenn es ressourcenschonend und gleichwohl zielführend geplant und auf die Anforderungen aller entscheidenden Unternehmensebenen hin optimiert ist, steht einem profitablen Digitalisierungsprojekt nichts mehr im Weg. Wird dem Netzwerk diese Bedeutung bereits beigemessen?
Was ist heute in Industrieanlagen der Status Quo? Bei der Steuerungs- und Netzwerkkonzeption in Maschinen und Anlagen wird in erster Linie auf die Umsetzung der geforderten Funktionen geachtet. Es überwiegt dabei das SPS-Konfigurationsdenken, beispielsweise bei der Verwendung von PROFINET. Die I/O-Module, notwendige Bedien- und Meldesysteme, Scanner oder auch Kameras werden funktional entsprechend der örtlichen Gegebenheiten verbunden und in der SPS-Konfiguration hinterlegt. Die Infrastruktur wird daher auf Basis des PROFINET-Zertifikats ausgewählt, wobei zusätzlich Preis und Herstelleraffinität im Fokus stehen. Lastermittlungen, Bandbreitenplanung und Performance-Festlegungen zur Infrastruktur werden nicht angewendet. Grundsätzlich ist gegen diese Herangehensweise nichts einzuwenden, denn Sicherheit, Funktion und Stabilität sind realisiert. Nicht berücksichtigt werden dabei jedoch die möglichen Digitalisierungsvorhaben des Betreibers, die nach zusätzlichen Produktionsdaten aus dem jeweiligen Fertigungsprozess lechzen (Bild 1).
Fehlender Dialog zwischen Maschinenbauer und -betreiber
Aktuell schließt der Maschinenbauer in der Konzeption seines Netzwerkes den Digitalisierungswunsch auf Betreiber-Seite völlig aus. Er betrachtet vorrangig die Funktionalität und legt das Netzwerk somit nur für eine Applikation aus. Dabei richtet er sich z.B. nach den geltenden PROFINET-Richtlinien und hält die geforderten Qualitätsparameter ein, z.B. der PI (PROFIBUS & PROFINET International). Er macht das, weil ihm jegliche Information über gewünschte zusätzliche Daten oder auch anstehende Digitalisierungsprojekte fehlt. Selten ist dies in einer Spezifikation beschrieben oder wurde auf eine andere Art und Weise kommuniziert. Das ist ein großes Manko und nicht selten ein Hemmnis für den Erfolg der Digitalisierungsprojekte, weil die Datenquelle „Maschinen-Netz“ verborgen bleibt.
Ein weiteres Problem liegt in der praktischen Erfahrung, dass der zusätzlich verursachte Traffic durch azyklische TCP/IP-Kommunikation plötzlich nicht-reproduzierbare Funktionsstörungen verursachen kann, denen meist durch Abschottung und Trennung begegnet werden konnte. Dadurch werden wichtige Datenquellen unbewusst verschlossen, die nur durch Inanspruchnahme zusätzlicher Ressourcen und Kosten – zweites Netzwerk und zusätzliche Sensoren – kompensiert werden können (Bild 2).
Fallbeispiel Energiemanagement
Dass Industrie 4.0 mittlerweile ein Erfordernis ist, ist unumstritten. Da das Maschinen- und Anlagennetzwerk erfahrungsgemäß als direkte Datenquelle aus den bereits beschriebenen Hintergründen nicht in Betracht gezogen wird, werden Daten auf zwei anderen möglichen Wegen gewonnen. Die erste und sehr verbreitete Möglichkeit ist der Weg über das Prozessabbild der SPS. Abgesehen davon, dass diese Daten oft aus Verknüpfungen bestehen, mit Zeitverzug gewonnen werden und einen zusätzlichen Programmieraufwand erfordern, stellt die SPS oft die benötigten Daten überhaupt nicht bereit. Diese Erfahrung machte ein Unternehmen bei der Erfassung von Energieverbrauchsdaten. Solche Daten werden sowohl in der Instandhaltung benötigt, um über den Unterschied von tatsächlich verbrauchtem Strom und Nennstrom der Verbraucher ein Verschleißabbild zu generieren, als auch im Bereich Umwelt- und Energiemanagement, der teure Lastspitzen vermeiden will. In diesem Fall wurde ein separates Netzwerk mit zusätzlichen Sensoren in Form von Verbrauchszählern installiert (Bild 3). Es wurden also zusätzliche Investitionen getätigt, statt vorhandene Ressourcen zu nutzen.
Die Unwissenheit über das eigentliche Leistungsvermögen des installierten Maschinen- Netzwerks erforderte zusätzliche Ressourcen, weil vorhandene ungenutzt bleiben. Über das PROFINET-Profil „Profi-Drive“ können direkt aus jedem Frequenzumrichter Stromwerte feingranularer (antriebsbezogener Verbrauch) ermittelt und in einem standardisierten Datenformat zur Verfügung gestellt werden. Würde man in einem frühen Projektstadium proaktiv mit dem Anlagenbauer diskutieren, würde recht schnell klarwerden, dass das Maschinen-Netzwerk diese Daten direkt bereitstellen kann und soll.
Fallbeispiel Condition Monitoring
Eine Maschine benötigt für das Condition-Monitoring circa 100 zusätzliche Sensoren, um den Abnutzungsgrad von stark dynamisch beanspruchten Baugruppen zu ermitteln. Um das Maschinennetzwerk nicht zu belasten, bzw. aus Angst ein erhöhtes Lastaufkommen zu generieren, wurde ein separates Netzwerk aufgebaut. Da die dafür kalkulierte Investitionssumme von 200.000 € fast aufgebraucht war, hat man die Anzahl der Sensoren auf 20 zusammengestrichen, letztlich wurden nur 5 Sensoren als Datenquelle eingebunden. Das Digitalisierungsprojekt wurde also „auf Sparflamme“ ausgeführt und hat letztlich nicht den geplanten Effekt gebracht: Budget eingehalten! Ziel erreicht?
Das Netzwerk als Ganzes betrachten
Bei allen Diskussionen zur Umsetzung von Digitalisierungsprojekten wird das Netzwerk ausgeklammert. Entweder, weil es vorausgesetzt wird, oder es wird in die Kostenkalkulation als notwendige zusätzliche Aufwendung integriert. Diese Betrachtungs- bzw. Herangehensweise muss sich ändern, wenn die Kosten den Effekt nicht eliminieren sollen. Vor allem bei Greenfield-Anlagen muss bei Digitalisierungsprojekten dem Netzwerk, seiner Planung und letztlich seiner Auslegung ein höherer Stellenwert eingeräumt werden. Das Netzwerk ist das verbindende Element zwischen dem, der Daten fordert und der Datenquelle. Eine ganzheitliche Betrachtung unter Berücksichtigung der unterschiedlichsten Applikationen und somit erforderlichen Bandbreiten ist der Garant für die durchgängige Kommunikation und die Erschließung verschiedenster primärer Datenquellen. Autark entstandene, abgeschottete Maschinen- und Anlagennetzwerke haben im Zeitalter der Digitalisierung und der damit verbundenen Projekte keinen Platz mehr. Die Netzwerke müssen planvoll geöffnet werden, ohne Sicherheit, Stabilität und Zuverlässigkeit aufs Spiel zu setzen. Sie müssen losgelöst von der Applikation betrachtet, spezifiziert und als Gewerk so ausgeschrieben werden, dass sich darin alle Belange der IT und der OT inklusive des Maschinennetzwerks widerspiegeln (Bild 4). Die somit entstandene Offenheit und Durchgängigkeit lassen Datenquellen erschließen, Kosten reduzieren und die Effektivität der Digitalisierung enorm erhöhen.
Damit ein solches Vorgehen in Zukunft einfacher wird, setzen sich die Netzwerkspezialisten von Indu-Sol heute intensiv mit dieser Thematik auseinander. Sie haben es sich zur Aufgabe gemacht, im engen Austausch mit den Betreibern von OT-Netzwerken die unterschiedlichen Netzwerkebenen ohne Hürden und Barrieren zusammenzuführen und die „Datenschätze“ aufzuzeigen. Die Netzwerkspezialisten als Projektbegleiter machen den Errichter mit den Anforderungen an das Maschinennetzwerk vertraut und erarbeiten gemeinsam mit ihm die erforderlichen Strukturen. Die Basis dafür bilden klare Regeln, die von IT und OT gemeinsam definiert und umgesetzt werden. Alle Vorgaben müssen geplant, kontrolliert, überwacht und die Verantwortlichkeiten festgelegt werden. Dann lässt sich der verborgene „Datenschatz“ heben. Der schonende Umgang mit Ressourcen ist ein wichtiger Bestandteil von profitablen Digitalisierungsprojekten.
Autor(en): Karl-Heinz Richter (Bild 5), Geschäftsführer für Marketing & Vertrieb Indu-Sol GmbH und Ellen-Christine Reiff, M.A. (Bild 6), Redaktionsbüro Stutensee ( www.rbsonline.de )
Weitere Informationen zum Thema finden Sie unter: