Network maintenance - a game of chance?
27.03.2023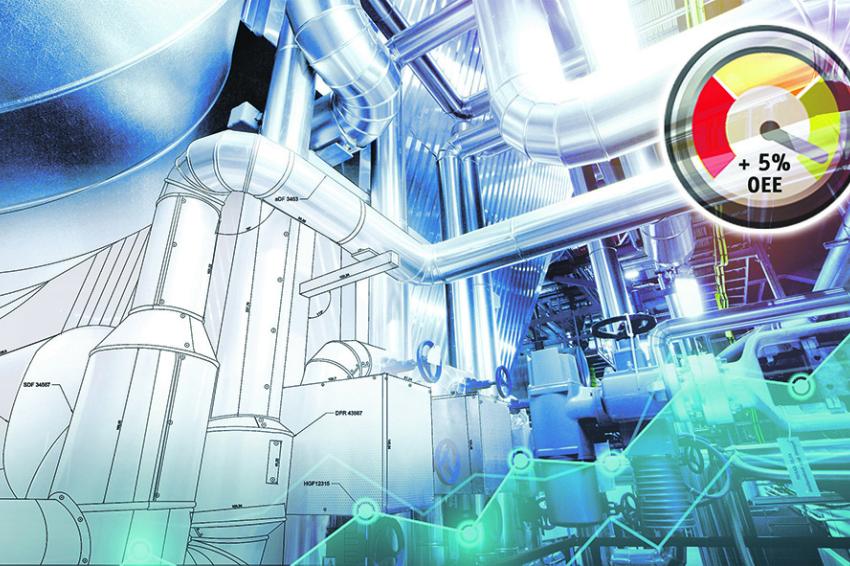
Errors aren’t talked about. But in relation to the overall equipment effectiveness, or OEE for short, it is essential, not only to talk about setscrews for process optimisation, but also to proactively point out and remove causes of (potential) plant stoppages. Condition monitoring is the keyword and in addition to monitoring the individual plant components (such as sensors, actuators, etc.) the communication network is also covered (including cables, connectors, etc.). Because in the network it is possible to detect the causes of unscheduled plant stoppages early, which can cost five to seven-digit sums per hour, depending on the industry. Especially in relation to brownfield plants, the question arises as to how digitalisation projects can be implemented so that investments for condition monitoring are amortised as quickly as possible through failure-free production.
What is the true specific value of error savings? How can the investment costs be justified to the management? Questions that the network experts of Indu-Sol can answer with empirical values acquired from their longstanding work. They have around 400 network maintenance deployments a year to attend. A good 150 of these are emergencies, i.e. the network experts are called out because of an unscheduled plant standstill. Nonetheless, many automation companies take the daily “reactive maintenance bet”, as the network experts call it. Because costs for investment in network monitoring can only be communicated to the management convincingly if the resulting savings or profits are clearly visible. The OEE is best influenced positively through high plant availability.
„The return on investment for a condition monitoring management system can be achieved quickly.“
Karl-Heinz Richter, Managing Director, Indu-Sol
Facts and figures
Ultimately, the investment and the “harvest” of a CMMS (Condition Monitoring Management System) is an expected value calculation in which, among other things, the probability of unscheduled plant standstills, their duration and the costs for the downtimes, inefficiently used personnel and lost material are input. Two practical examples clearly show how the breakeven for this investment can be achieved. The main costs in the calculation are incurred due to the average downtime costs.
On the one hand, we consider the application of automated control of a mineral well for mineral water treatment and on the other hand a production facility in the pharmaceutical industry (Figure 1). Let’s assume that both plants produce 24 hours a day, 365 days a year. If we deduct scheduled standstill times and assume a failure rate of 0.0075 %, a realistic value for the unscheduled plant stoppages per year is 65.7 hours. In the first case the average downtime costs are 10,000 euros per hour, in the second an estimated 1.5 million euros. Thus, for the well, the annual downtime costs and thus the unscheduled maintenance costs amount to 657,000 euros; for the pharmaceutical production facility they are an eye-watering 98,550,000 euros. In both examples it seems almost absurd to offset the investment costs for a CMMS. We do it nonetheless for the purposes of completeness and assume a similar network size with 15 controls for both examples. The costs involved are thus 120,000 euros for the initial investment in hardware and setting up the CMMS software and annual licence costs of 13,800 euros for the software.
DIn both applications, the investment is not only amortised in the first year, but also a “condition monitoring harvest” is brought in. In the case of the well application it is 471,000 euros in the first year and then 579,000 euros from the second year. The “harvests” in the pharmaceutical application are far more drastic with a good 88 million euros. A CMMS therefore pays, above all because it is applied to the largest “attack vector” namely that of plant availability. The questions that remain to be answered are: How does it work and how reliably are anomalies identified?
Four pillars for efficient network monitoring
The OEE of a production facility is made up of availability, performance and quality. Indu-Sol’s CMMS has a direct influence on the first two parameters, because it helps to avoid plant stoppages, to make ageing processes visible early and to enable preventive intervention. The aim of a CMMS for the network is to detect anomalies in the communication before they become a real problem. The causes are often sporadically occurring and can only be found, understood and removed by consistent monitoring. The Thuringia network experts offer a CMMS not only for Profibus but also for Profinet or ethernet IP. The solution for Profinet/ethernet IP is described in greater detail in the following. It consists of four pillars, which contribute to reliable network monitoring:
The first mainstay are the intelligent industrial switches of the PROmesh P series. With their integrated online line diagnosis and monitoring features, they help to identify problems in the network communication. Around 40 percent of all anomalies such as wear in cables and connectors as well as network load, errors, discards and jitter (by the way, jitter is the first indication of pending faults) can be found with the special switches - compared to off-the-shelf switches, this is a factor of three. The second pillar is then formed by the PROFINET-INspektor, which monitors the application itself rather than the network, and there it finds around 50 percent more of the causes for anomalies, such as jitter, telegram gaps or logouts. The collated information is then bundled and analysed in the PROmanage NT software (the third pillar). Finally, the fourth pillar is the human, who uses the available information to initiate appropriate measures. This can either be a trained maintenance employee in the company or a service technician from Indu-Sol. The increasing shortage of skilled personnel, which also does not leave maintenance departments unscathed, is definitely a contributing factor to the observations made by the network experts, which could become a trend: The outsourcing of network communication to external service providers.
The solution for the Profibus functions similarly, only due to its function it does without the first pillar – i.e. the switches. Overall, the Profibus CMMS finds around 80 percent of the anomalies that can lead to faults.
„Network monitoring and diagnostic functions provide a complete overview of systems and network sections.“
Tim Creutziger, Product Manager & Team leader Industrial Switches, Indu-Sol
Digitalise brownfield plants cost-effectively and securely – the 5th pillar
Reliable operation and increasing the OEE is a topic that also affects brownfield plants especially. In many cases, they are like black boxes on whose OEE few statements can be made. As of now, however, it is difficult to digitalise them cost effectively so that you have access to the process variables with an accuracy necessary to increase the overall equipment effectiveness. On the one hand this is due to the lack of sensors to read out the necessary process variables. On the other hand, existing communication networks would also be overwhelmed by the task of transferring these data in addition to the data necessary for the process control.
From the spring of 2023, Indu-Sol counters this challenge with its SIEDS sensors. The multi-functional sensors register numerous different maintenance-relevant variables such as temperature, vibrations, brightness and acoustics. To relieve the communication network, these data are then transferred directly on the IIT level (Industrial Information Technology), in which the PROmanage NT network management software also works, and which bundles these data, reports anomalies and uncovers optimisation potential. To enable this, all switches are connected in series beforehand. To avoid problems with IP duplications, the network experts have developed a corresponding “digitalisation bridge”, which enables the separation of data for the process control and for the maintenance. The network remains homogeneous and only allows the sensor data to pass through. This concept manages to solve and satisfy both apparently opposite demands of the users: That of network opening by coupling the switches and that of security thanks to the bridge. In this way, brownfield plants can be digitalised cost-effectively without extensive or expensive retrofitting on the network level. At the same time, the maintenance provider can now monitor the plant more reliably and get to the bottom of problems proactively. Other solutions on the market are based on setting up completely new communication networks. Here the network experts deliberately opt for a cost-effective, customer-focussed approach.
Machine builders and plant operators benefit
As a manufacturer of components for a reliable communication infrastructure, the network experts are interesting not only for machine builders but also for plant operators. Because on the one hand they provide support at the decision-making stage in the concept phase and network planning. On the other hand, they offer services for maintenance and management of the network during the use phase. Both the products and the services of the network experts are based on almost 20 years of practical experience with the preventive diagnosis of networks and emergency deployments. This know-how and tools such as the CMMS enable plant operators to no longer have to opt for the expensive and risky “reactive maintenance bet”.
Authors: Karl-Heinz Richter, Managing Director, and Tim Creutziger, Produkt Manager Industrial Internet and Team leader Industrial Switches, Indu-Sol GmbH, Schmölln
Further information on the topic can be found at: www.indu-sol.com/en/condition-monitoring
Author: Kathleen Klehm