PROFINET on the advance
Volkswagen AG Emden
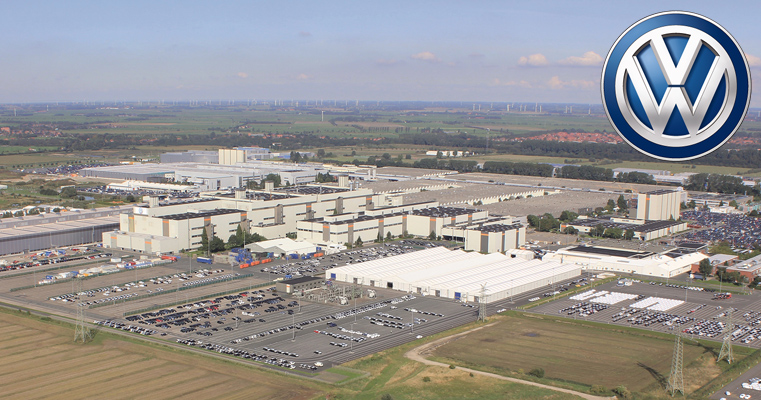
Volkswagen Emden relies on know-how from Indu-Sol
According to Profibus & Profinet International (PI), more than 9.8 million PROFINET nodes were installed worldwide at the end of 2014. And there is no end in sight. Most new systems are built with this standard, while older ones are being retrofitted. Experiences with PROFIBUS show that intelligent planning and monitoring are important tools to ensure system availability. The management of the Volkswagen factory in Emden recognized this and relied on the support of Indu-Sol from the start.
The Volkswagen factory in Emden is the largest industrial employer in the area of Germany west of Bremen and north of the Ruhr Valley. In addition to the Volkswagen saloon car and the Passat hatchback, the factory also produces the Volkswagen CC, Passat GTE, as well as the Passat Alltrack. At a daily production output of about 1,250 vehicles, the stability of the systems running the assembly has to be ensured at all times. To be able to plan and monitor system availability, the Volkswagen factory in Emden has been migrating to the new PROFINET standard step by step since 2011. Julian Kyek of the technical office in charge of assembly line maintenance explains: „To get to know the technology, we started out with a reference system that is running parallel to production without being directly involved in line operations. The systems required for the B8 are being configured for PROFINET right from the start.“
Following experiences with PROFIBUS and the insight that any technology may be vulnerable to environmental impact or internal irregularities, Volkswagen contacted Indu-Sol GmbH for implementing the new systems. „We‘ve been in touch with Indu-Sol since 2005. Based on our experiences with PROFIBUS, we began to study PROFINET well ahead of making the switch. Together we drafted criteria for new systems that we put into the product requirements documents. For example, one requirement is that each system must have a PROFINET-INspektor® so that we can test the quality characteristics of the PROFINET segment“, explains Mario Ewen, in charge of electrical systems in the assembly maintenance unit.
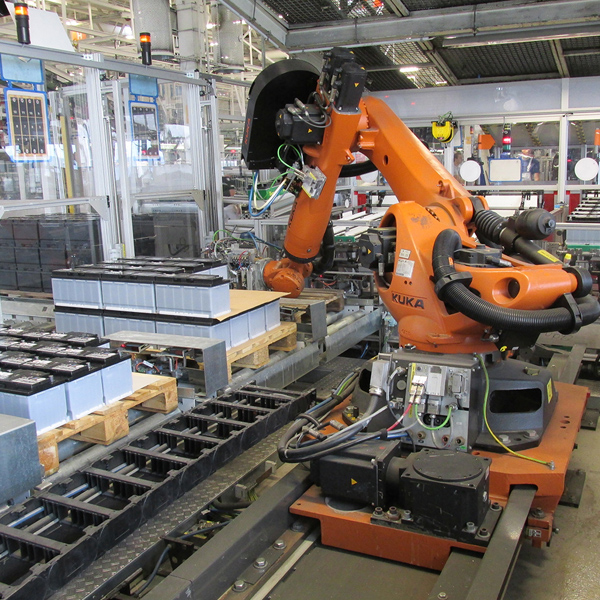
Battery assembly is used as the reference system, i.e. the first system that was built with PROFINET. The PROFINET-INspektor® is silently watching
Indu-Sol developed its PROFINET-INspektor® for acceptance test and testing of new systems and for long-term monitoring. With an on-board TAP, it is both a fully featured measuring device and an intelligent measurement point.
As a „silent observer“, the PROFINET-INspektor® provides insights into parameters such as utilization rate, data throughput, update rate, telegram gaps and telegram jitter. Trigger functions with permanent settings respond to changes in the network. A potential-free contact sends an alarm when any of the configurable thresholds is exceeded. This provides information of the actual state of communications quality in the network at all times. An integrated web server enables the information to be displayed on any PC with a browser program. Simple colour-coded representations of the network condition (red, yellow, green) enable quick and user-friendly operation of the device as well as the evaluation of events. Data storage on the device makes this information available for later review.
Horst Voigt, Key Account Manager Automotive at Indu-Sol, describes additional functions of the INspektor®: „The INspektor® also functions as a passive data logger. It is permanently installed in the network, where it is able to continuously monitor the logical telegram exchange during production. The system operator is aware of the network condition at all times and can initiate countermeasures before the bus system crashes and the production line stops.“ Continuous analysis of the network condition is indispensable for ensuring real-time PROFINET communications and to keep aware of the volume of extraneous communication. „Preventative maintenance is critical for us. We implemented the INspektor® to be able to respond before a line goes down. Now we get advance warning of weaknesses in the system, and are able to fix them independently“, Julian Kyek says.
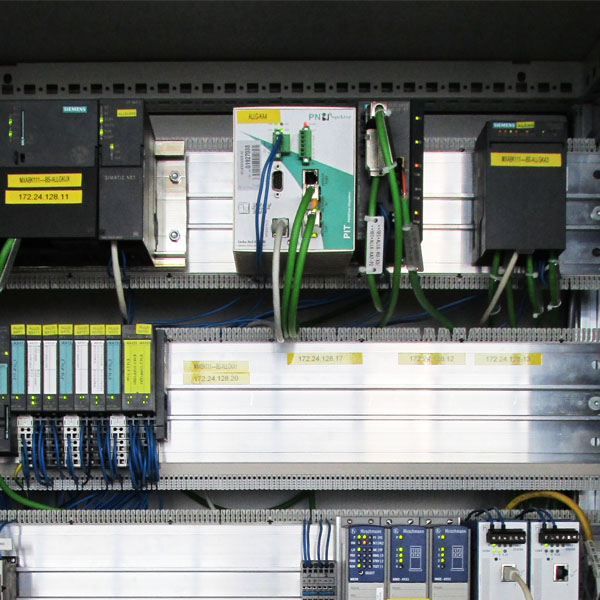
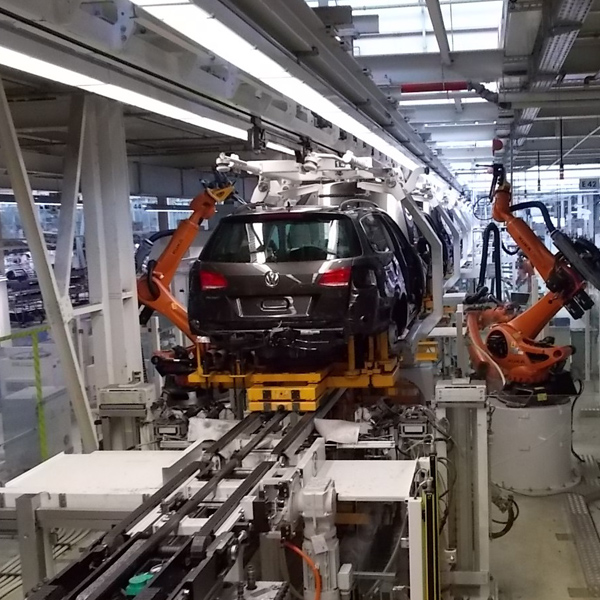
In conjunction with the PROscan® Active topology software, the PROFINET- INspektor® operates like a navigation system for the PROFINET network. PROscan® Active scans the PROFINET network during running operation and creates a graphical topology map. It contains information about the PROFINET name, the IP and MAC address, the current port assignment, cable lengths and attenuation reserves for polymer fibres, and information about interrupted communications. The software also provides device information like hardware and software version or device name and type in an easy-to-use list. In conjunction with the PROFINET-INspektor® diagnostic device, the topology map delivers information about the condition of each device at a glance.
PROscan® Active is currently being tested at the factory in Emden. To unify the standard, all future new or retrofitted systems will be configured for PROFINET. Mario Ewen points out: „Most of the errors in a bus system are committed during its installation. That‘s why it is important for us to have our systems tested by an independent partner before commissioning so that we can eliminate a majority of the errors that may occur later during operation.“
In order to be able to respond appropriately when needed, all concerned employees are trained in PROFINET diagnostics at the Volkswagen Academy by experts from Indu-Sol. To combine theory with practice, employees of the Volkswagen factory observe the system measurements on site. „Indu- Sol have proven themselves to be reliable partners”, says Mario Ewen. The people in Emden are optimistic about the future prospects with PROFINET. His colleague Kyek summarises: „The new PROFINET systems are running very stable because we prepared them carefully. We haven‘t had a major incident yet.“ Indu-Sol will continue to be a reliable partner for future collaboration on the shores of the North Sea.
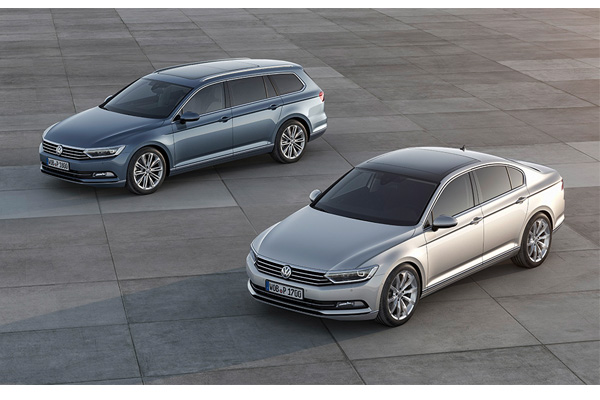
Any questions?
Our contact persons are at your service.