EMC and Network Performance
Challenges and Solutions in Mechanical Engineering
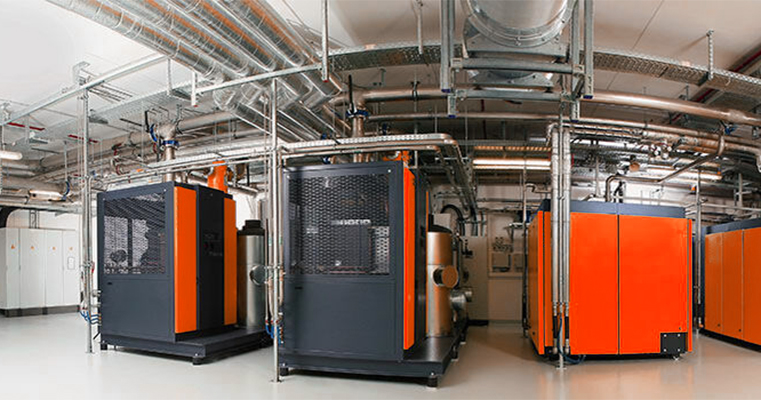
Challenges in Compressed Air Technology
Our client, a global leader in industrial compressed air technology, serves industries from food production to heavy manufacturing. Machine control requires Ethernet connections to individual compressors and access to sensor data (such as flow rate and temperature). Initially, the decision to use unmanaged switches was made for cost reasons; however, challenges soon became apparent due to outages and network disruptions.
Main Difficulties: Integration with Existing Networks
The main difficulties arise from integrating with the operators' existing networks, which often lie outside the control of the machinery manufacturer. Additionally, the responsibility for grounding lies with the operator, leading to unexplained outages and unplanned downtimes that caused significant disruptions in operations and decreased customer satisfaction.
The Black Box of Networks and Causes of Failures
A key pain point for machine builders is the "black box" of the customer network. Since the operator's network infrastructure is not fully visible or controllable, unplanned machine downtimes occur, making diagnostics challenging. This situation is especially critical for companies that heavily rely on machine availability. This 'black box' leads to significant costs from outages and complicates troubleshooting.
Without detailed on-site network information, the machinery manufacturer’s customer service team often struggled to pinpoint the causes of disruptions. Furthermore, many of the incoming reports required tapping into the limited resources of electrical engineers. A solution was urgently needed to improve service efficiency and reduce unplanned outages.
Objectives of the Machinery Manufacturer: Minimize Downtime, Increase Efficiency
The primary objectives of the machinery manufacturer were to minimize unplanned downtimes and enhance customer satisfaction. These outages, often caused by Ethernet communication issues and a lack of transparency between machines and the customer network, needed to be ideally eliminated.
Moreover, the goal was to reduce the reliance on specialized electrical engineers for service. Since these resources were not unlimited, improving network transparency and monitoring was essential for optimizing support.
Deployment of PROmesh P Diagnostic Switches for Fault Analysis
In critical installations, the machinery manufacturer employed the proven PROmesh P diagnostic switches to monitor network issues and identify fault sources early. These switches provided comprehensive information on electrical and logical network parameters that were otherwise missing in the service process.
Particularly in cases of sporadic outages, a clear cause was identified: electromagnetic interference (EMC). Data analysis revealed that leakage currents were flowing through the shields of the Ethernet data lines, leading to network disruptions and device failures.
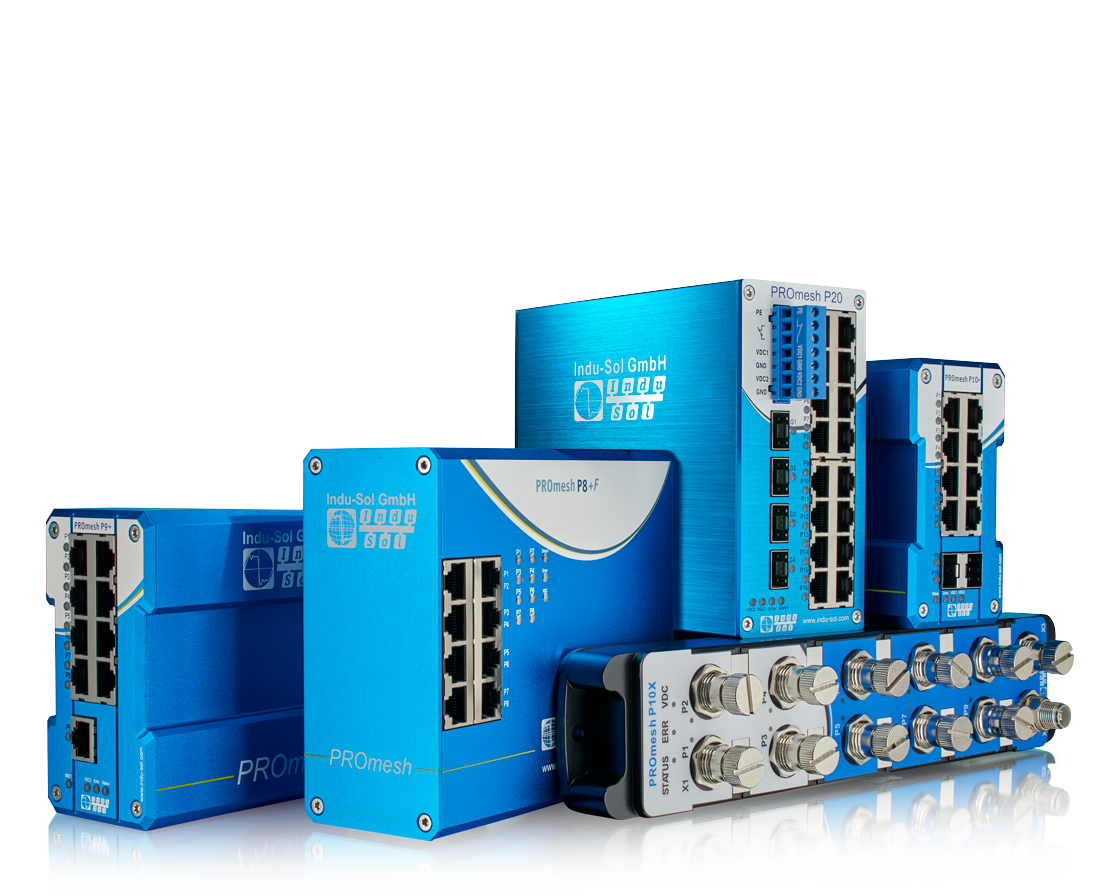
EMC Issues: A Complex and Costly Problem
A common cause of EMC issues was the star topology of the grounding system. Long cables and high impedance in the grounding system led to the diversion of currents onto the data lines and connected devices. These devices were not designed to handle such disturbance currents, resulting in faster damage, sporadic restarts, or complete failures.
The solution was to identify these causes and collaborate with the operator to improve the grounding system. Indu-Sol provided expertise and technical solutions to make the grounding system more effective for handling leakage currents and permanently eliminate disturbances caused by EMC.
Meshed Equipotential Bonding as a Solution
By implementing the EMClots® system, the equipotential bonding system could be significantly meshed. This reduced impedance and prevented currents from affecting sensitive devices via the data lines. This was especially critical in environments with high-power machines like compressors and motors, helping to avoid future disruptions.
New Service Requirements: Digitalization and Remote Service
Alongside the physical challenges posed by EMC, further obstacles were emerging for the company: business continues to grow rapidly, but due to a shortage of skilled labor, maintaining global service is becoming increasingly difficult. Additionally, complexity at the network level is rising as sensors become more digitally interconnected. This increased network load could potentially lead to new problems.
Starting in 2025, fully managed industrial diagnostic switches from the PROmesh P family will be deployed across all stations, offering not only EMC monitoring but also a range of other diagnostic functions, such as continuous monitoring of line quality and network utilization. These devices enable remote monitoring, reducing the need for specialized on-site personnel and allowing 60% of network problems to be diagnosed and resolved remotely.
Products used
Subscribe to our newsletter
Stay informed! Receive the latest offers and news about industrial networks and their optimization - conveniently via e-mail.