Find out more, enjoy a free trial and benefit:
Automated condition monitoring of data lines, avoidance of line-related malfunctions
Functioning data lines are the basis of modern industrial plants. If cables are worn or defective, entire machine processes are affected. However, conventional maintenance of data lines is often neglected. Too difficult, too expensive, no time. Yet almost every industrial data line has to be maintained or renewed sooner or later. But how can maintenance costs for data lines be kept low?
The clever solution: Monitor heavily used or hard-to-reach data lines permanently without additional personnel effort.
7 reasons for condition monitoring of data lines:
Why online line diagnostics is worthwhile for you
- Increase system availability without additional personnel
Reduce line-related downtimes - whether planned maintenance or due to defective line routes. - Detect line-related malfunctions at an early stage (including hard-to-find malfunctions)
Detect critical line conditions before malfunctions become apparent - without additional personnel effort. - Find data lines that require replacement without manual cable measurement (port-accurate)
No more need for time-consuming and personnel-intensive cable tests to locate defective data lines. - No unnecessary maintenance work on difficult-to-access data lines
Reduce time-consuming and possibly dangerous maintenance work to a minimum - Reduce material costs for PROFINET and Industrial Ethernet cables
Only replace data cables that have actually reached their wear limit. - Straightforward maintenance strategy for line routes
Maintain your data cables with foresight for the first time - condition-oriented and resource-saving. - Can be retrofitted in any PROFINET / Industrial Ethernet-based system
Integration at network nodes (switches) for maximum practical benefit
Find out more about the advantages and possible applications of the data line monitoring "Online line diagnostics". Request information now.
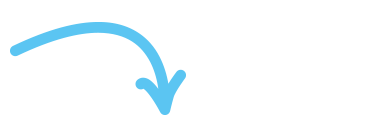
Would you like to find out more?

The operating principle explained briefly and succinctly

Why monitoring is worthwhile. (Example calculation)

Outdated methods cost time and money

Which devices can be used for this purpose?
Technology explained: Data line monitoring during operation
How does "online line diagnostics" actually work?
The "online line diagnostics" developed by Indu-Sol is based on an evaluation system of the transmission and reception parameters of connected data lines. In addition to the SNR value, which is also recorded by manual cable test devices, additional measured values of the active data communication flow into an evaluation matrix. In contrast to manual line tests using cable testers, the "online line diagnostics" is carried out continuously during ongoing system operation.
The basis for evaluation is a calculated actual value, which is compared to a target value corresponding to the cable length. Depending on the ratio of the two determined quality values, a so-called "wear reserve" of the respective data cable results. If this falls below the preset (or individually adjusted) threshold, a status warning is triggered. This can be displayed via the PROmesh switch's web interface, email notification or integration into a higher-level network monitoring system.
The responsible maintenance technician can then quickly locate the worn PROFINET or Industrial Ethernet data cable and replace it in a planned manner. Thanks to the data cable monitoring, the maintenance technician can identify the affected data cable in a matter of seconds - without manual cable measurement.
Example calculations: Savings potential through online line diagnostics
Is line monitoring economically worthwhile?
Initial situation
- PROFINET system with 5 drag chains
- Planned system operation tim: 10 years
- Service life of a drag chain: ca. 2 years (approx. 2 million bending cycles to the wear limit)
≙ 4 changes per drag chain during the planned service life - Replacement of the drag chain takes place in case of wear-related downtime (unplanned line malfunction)
≙ min. 20 downtimes for maintenance work on drag chains
Savings potential with "online line diagnostics"
Costs for downtime (due to malfunction) | € 200 per minute of standstill |
Ø downtime (drag chain defect) | 90 minutes |
Downtime costs over plant operating time (without online line diagnostics) | € 360,000 (200 € x 90 min) x 20 drag chain replacements |
Ø Investment costs PROmesh switch (with online line diagnostics) | € 5,290 Ø € 1,000 €1 x 5 drag chain sections2 Ø € 290 Installation costs3 (€ 58 per switch) |
Savings potential | € 354,710 Downtime costs - investment costs PROmesh |
Please note:
• Additional expenses due to previous sporadic malfunctions or maintenance-related manual line checks have not been taken into account. These costs are to be added to the downtime costs, if applicable.
• No additional downtime costs for installation of the PROmesh switches, as possible within regular maintenance shutdowns
1 Investment costs per switch vary depending on the PROmesh switch required and the number of switches
2 Maximum number of switches required; depending on the system topology, fewer switches may be required
3 Includes installation and configuration (max. 2h), actual costs depend on your maintenance staff costs
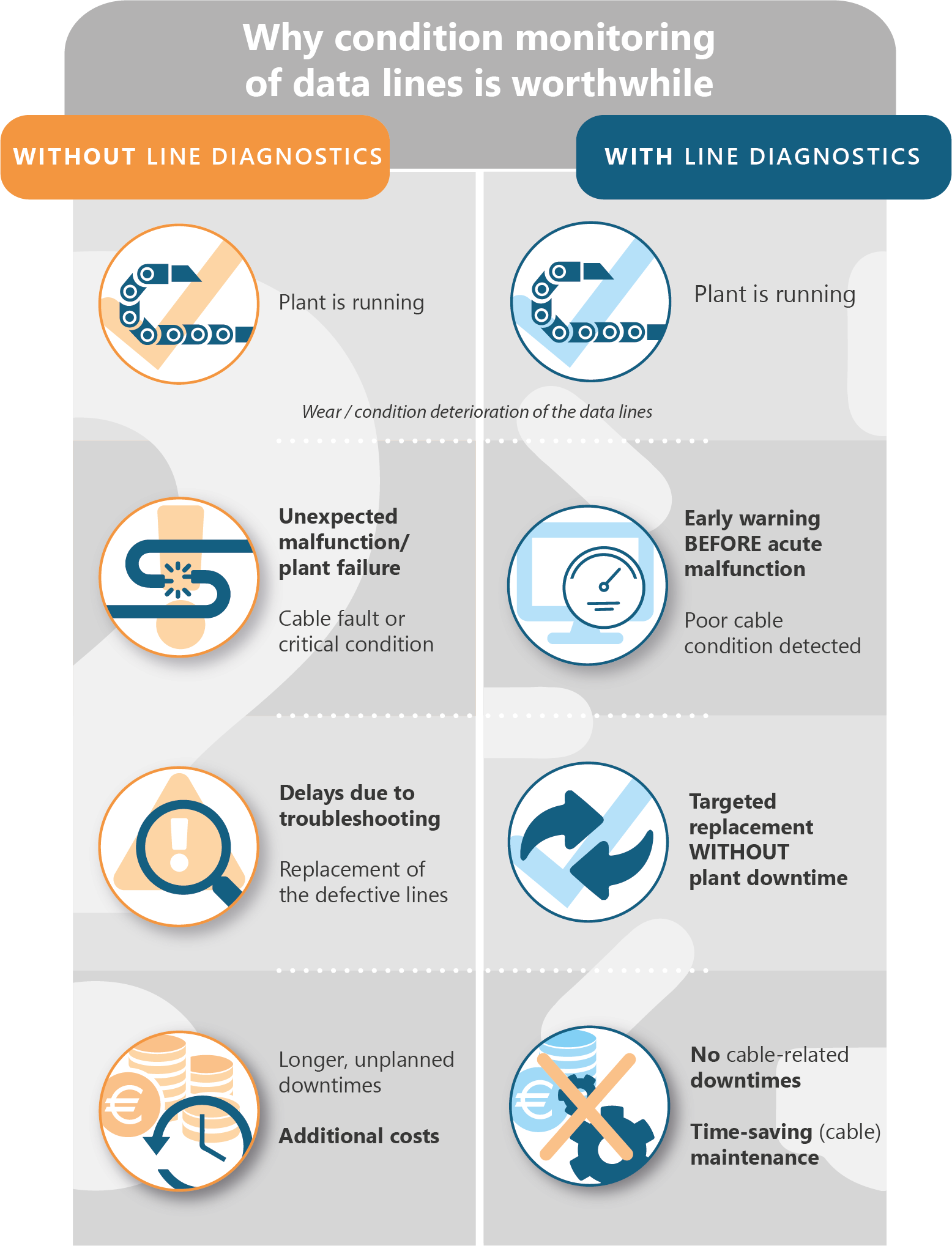
Interested?
Request more information about the innovative online line diagnostics.
Sad everyday life in the field
Outdated "maintenance strategies" for industrial data lines
In order to avoid line-related malfunctions or plant downtimes, many industrial companies still rely on outdated and unnecessarily complicated methods. We would like to use two examples to illustrate that it makes sense to critically question formerly tried and tested procedures.
Maintenance strategy "Manual cable test"
(high personnel and time expenditure, only possible during system downtime)
Without permanent monitoring, the current status of a data line can only be determined manually during a downtime phase. These manual cable tests are very labour- and time-intensive. Especially since all data lines to be tested must be measured from both sides. Due to the considerable effort involved, such cable tests are usually only carried out for commissioning and in the case of line-related troubleshooting.
Maintenance strategy "replacement of functioning data lines"
(high material costs, not very resource-saving, only possible during plant downtime)
In order to avoid line-related malfunctions, functioning lines are regularly replaced in many industrial companies as part of routine maintenance. As a result, line sections are renewed even though they would still continue to function without any problems. Often it is not checked whether the replacement was necessary, as feared unplanned downtimes would have resulted in higher costs.
Do you recognise yourself? Relieve your maintenance and increase your plant availability. We support you in the changeover of your maintenance strategies. Please talk to us!
Our recommendation
"Automated monitoring of data lines"
(low personnel and time expenditure, during plant operation, resource-saving)
Data lines, especially in heavily used plant areas, are permanently monitored by means of "online line diagnostics". If the condition falls below a critical value, the responsible maintenance department is automatically notified and can schedule a replacement of the affected line section. This allows unplanned plant downtimes caused by defective data lines to be avoided in advance.
Thanks to the port-accurate online line diagnostics, defective data lines can be selectively replaced without manual cable tests for localisation.
Condition monitoring for data lines in PROFINET/Industrial Ethernet systems
How to use permanent line diagnostics in your plants
To use the automatic condition monitoring of your PROFINET or Industrial Ethernet lines, you need industrial switches with integrated "online line diagnostics". Thanks to the function integrated in the industrial switch, connected lines are monitored with port accuracy and changes in status are documented. If a monitored data line reaches a critical state, you are automatically notified and can react at an early stage.
Use the following PROmesh Industrial Switches to monitor your data lines:
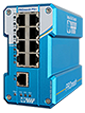
PROmesh P9+
Industrial Switch for control cabinet
- IP20 cerrtified
- integrated network disgnostics and monitoring features
- 9x RJ45 ports (up to 1,0 Gbps)
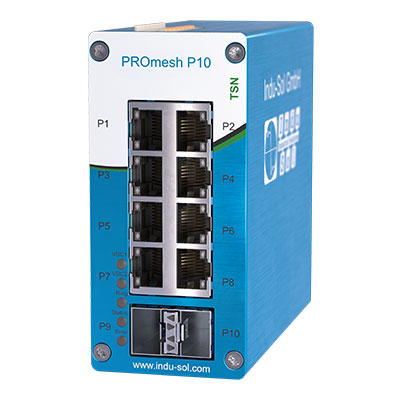
PROmesh P10
Industrial switch for control cabinets
- IP20 certified
- integrated network diagnostics and monitoring functiones
- 8 x RJ45-Ports (up to 1.0 Gbit/s)
- 2 x SFP-Slots (up to 2.5 GBit/s)
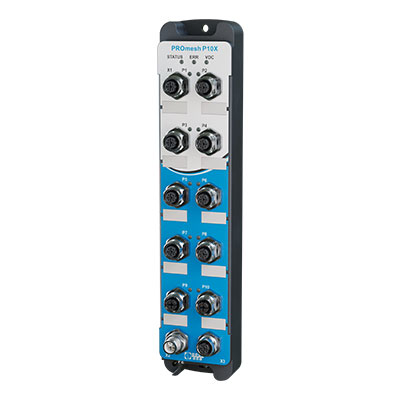
PROmesh P10X
Industrial switch for harsh environments
- IP67 certified (waterproof/dustproof)
- integrated network diagnostics und monitoring functions
- 8 x M12 D-coded (up to 100 Mbps)
- 2 x M12 X-coded (up to 1.0 Gbps)
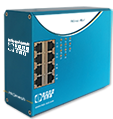
PROmesh P9+
Industrial Switch for control cabinet
- IP20 cerrtified
- integrated network disgnostics and monitoring features
- 9x RJ45 ports (up to 1,0 Gbps)