Discharge current
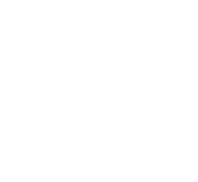
The more intensive the application of electric drive and controller technology in the industry becomes, the more likely that discharge currents occur. In particular in automated production – with its increasingly quicker cycle frequencies and signals with steepness edges – discharge currents can occur whose frequency bands extend from the "manageable" Hz range to the difficult to monitor MHz range. Parts of these increased discharge currents can also be found in the PE conductor currents. Thus a correlation can be established between discharge currents and network failures: If discharge currents occur for instance in the shield connections of the industrial network infrastructure, they can cause voltage differences in the reference potential and destabilise the equipotential bonding (PA). There would be no stopping of interfering EMC influences into the data communication in the industrial network.
When machines or plants are being operated, discharge current is generated due to capacitive coupling of electric components and also especially because of inductive coupling between two of more conductors. Why does this happen?
In contrast to residual and discharge current is therefore due to operation and cannot be avoided completely. As long as it remains within certain limits, it endangers neither availability nor operational safety. Dedicated constructive measures on the plants – such as the optimisation of the equipotential bonding system and the routing of cables – but also regular checks make sure that these limits are maintained.
Keyword: Limit values for discharge current
DIN VDE 0701-0702 specifies the limit values for electric mobile equipment. Accordingly, discharge current, as touch current, must not exceed a current of 0.5 mA. For discharge current as PE current, the limit value lies at 3.5 mA. Discharge currents with higher frequencies as they occur for example in automated production plants, may be several times the 3.5 mA. Standards such as the DIN VDE 0104 define specific limit values for currents with frequencies ≥500 Hz and ≤1 MHz.
Many electricians have been puzzled by discharge currents. A "popular" scenario evolves as follows: An earth-leakage circuit breaker that is installed in front of a frequency inverter (FI) is frequently triggering even though there is no obvious residual current. Machine or plant comes to a standstill anyway. Most common cause in such cases is increased discharge current. On the plus side: The expert can deduct from that that the insulations on the devices and equipment are in order. Because discharge currents occur only in fault-free circuits.
Less trivial but therefore not less common is the scenario with a red fault LED: If such a warning light flashes on the plant hardware, it indicates to the service technician that there is a malfunction. The diagnosis can now begin on site – he will, however, rarely find the cause for the malfunction directly at the signalising location. If data communication is affected, it possibly may not be possible to even locate a weak spot in the system. Then at the latest the question should be posed as to external influences such as electromagnetic incompatibilities. If such increased discharge currents should actually be taken into consideration as being the cause a malfunction, then it is not easy for a service technician to localise that. Only targeted measurements at the equipotential bonding system as well as at the shield connections of the bus lines bring the technician closer to the solution.
Operational loads on the equipotential bonding should basically be as low as possible. Suitable measuring devices are necessary to check the quality of the equipotential bonding and with that the EMC stability of industrial networks. The loop impedance measuring clamp MWMZ II operates with a fixed test signal frequency of 2,083 Hz and measures loop impedance resistance as well as discharge current at shielding and earth of machines or plants. Alarm thresholds for the measuring values can be preset. The current clamp signals a warning automatically in case the discharge current is quite distorted or values >5 A or >10 A are reached. By multiplying the loop impedance with the strength of the discharge currents, the MWMZ II also makes it possible to estimate the contact voltage – important information concerning operational safety.
In addition, the ISMZ I can be used to detect transient discharge currents that are difficult to verify. With sampling rates of 10 kHz, 30 kHz and 40 kHz, the intelligent current measuring clamp measures quicker and more precise than conventional current clamps. Additionally, it features an integrated memory to that it can also be applied for long-term measurements: For a duration of up to 14 days, it records and evaluates the current course automatically in the routed line. If the set threshold values are reached or exceeded, this event is recorded for later analysis. The corresponding analysis software EMCheck® View is already included in the scope of supply.
A continuous monitoring of discharge currents and other electromagnetic interference is made possible by EMV-INspektor® V2. Up to four measuring channels can be hooked up to the diagnostic device at the same time, e.g. power supply, motor line, data line and equipotential bonding line. Thus all important line paths of a machine or plant can be recorded and analysed in parallel. This facilitates the troubleshooting of EMC sources of interference, but also can prevent costly plant shutdowns. A basic discharge current monitoring is performed by the fully Ethernet-compatible PROFINET Switch PROmesh P9 from Indu-Sol: It is capable of permanently recording and evaluating the sum of all shielding currents of the connected lines. The corresponding spectrum with the respective frequency components is specified on its web interface in addition to the current value. Thus the switch provides important information on possible EMC interferences and with that all necessary information for a comprehensive network diagnosis.
Do you need assistance?
On request, our measurement technicians can come to your site to record leakage and leakage currents and evaluate the EMC conditions of your machines or systems.