Downtime costs
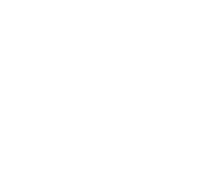
The financial consequences of plant downtime - whether planned or unplanned - should not be underestimated in the industry. Various sources report that one hour of unplanned downtime in the automotive industry now costs around €1.85 million dollars. Downtime costs of between €40,000 and €200,000 per hour are also not uncommon in fast-moving consumer goods (FMCG) or in the food industry. This article aims to provide a deeper understanding of how to calculate both tangible and intangible downtime costs while providing strategies for plant managers to minimize these costs and increase overall efficiency.
Unplanned downtime often requires employees to work overtime, which incurs additional costs. Overtime is usually paid at a higher rate than regular working hours. Let's assume that the normal hourly wage is €18.5 and the overtime rate is 1.6x, i.e. €29.6 per hour. For the repair of the production line over 5 hours by 6 employees, costs of around €880 are incurred.
Cost of the idle working hour: Occurs when employees are paid during a shutdown without being productive. These costs arise from the continued payment of salaries despite the loss of production and are calculated by multiplying the idle hours by the average cost per hour.
Example: A 2.5-hour downtime on a production line with 25 workers earning an average of €18.5/hour results in idle labor costs of €1,156.25 (25 workers x €18.5/hour x 2.5 hours).
Repair costs are incurred when downtime is caused by technical defects. They include expenses for spare parts, the deployment of specialized workers and the equipment required to rectify the problem and restore the system.
Intangible costs include:
Through strategic planning, the use of modern technology and the promotion of a proactive team, plant managers can not only minimize the direct and indirect costs of downtime, but also improve the overall efficiency and competitiveness of their company. Investing in downtime prevention is therefore not only a hedge against financial loss, but also a step towards a more sustainable and productive future and optimal overall equipment effectiveness (OEE).
The implementation of a Condition Monitoring & Security Management (CM&SM) system offers a variety of benefits for operators in the industry, especially in the areas of predictive maintenance and Operational Technology (OT) security. By detecting potential problems and security threats at an early stage, companies can not only minimize downtime and its costs, but also extend the service life of their equipment and ensure the security of their operational technology. Here are the key benefits of such a system:
1. Early fault detection: CM&SM systems enable continuous monitoring and analysis of the condition of machinery and equipment. By recording and analyzing data such as vibration, temperature and performance in real time, anomalies can be detected at an early stage. This enables preventive maintenance interventions before costly breakdowns occur.
2. Improved system availability: By reducing unplanned downtime through preventive maintenance, operators can significantly increase the availability and reliability of their systems. This leads to continuous production and avoids production losses.
3. Cost savings: Reducing downtime and avoiding serious equipment damage through early maintenance leads to significant cost savings. These savings result from lower repair and spare parts costs as well as from the optimization of maintenance schedules that reduce unnecessary inspections.
4. Increase OT security: CM&SM systems contribute to the security of operational technology by continuously monitoring network traffic and checking for anomalies. This helps to identify cyber threats and vulnerabilities at an early stage and initiate countermeasures to protect the integrity and confidentiality of critical industrial control systems.
5. Data-based decision making: By collecting and analyzing operational data, CM&SM systems enable informed decision making. Operators can make maintenance and investment decisions based on accurate data about the condition and performance of their equipment.
6. Improved safety and compliance: Another important benefit is improved safety for employees and compliance with regulatory requirements. By preventing accidents and breakdowns that can be caused by overlooked equipment problems, CM&SM systems help to make the working environment safer and meet compliance standards.
7. Long-term equipment optimization: The long-term collection and analysis of condition data provides an in-depth insight into equipment performance and wear patterns. This helps operators to develop optimization strategies for their assets, reduce lifecycle costs and increase overall efficiency. Overall, the integration of a CM&SM system into the operational strategy of industrial companies provides a solid basis for improving maintenance efficiency, increasing plant safety and ensuring greater system resilience to operational and safety risks.
Conclusion
The financial impact of downtime is significant and increasing. Experts estimate that the total losses due to downtime for an industrial company can amount to up to 11% of turnover. This compares with an average investment of around 3% in the maintenance budget. As the figures show, there is still significant profit potential to be leveraged in plants in the future if a forward-looking maintenance strategy is consistently implemented.
Stay informed! Receive the latest offers and news about industrial networks and their optimization - conveniently via e-mail.