Typical sources of EMC interference
in industry and automation
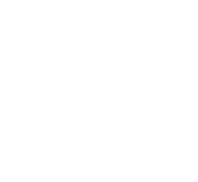
In recent years, many studies have revealed ever increasing loads on equipotential bonding systems due to highfrequency currents. The causes for this increase are quickly identified by the increasing number of variable-speed drives, combined with an increasing degree of automation of machines and systems.
Strong and higher-frequency currents, as generated by frequency inverters for example, are a main cause for EMC interference. The resulting field loads are illustrated in the following figure.
As soon as an electrical conductor is exposed to a changing magnetic field induction will result. In this instance, this results in a shield current on the bus line. This problem is widely known and efforts are made to minimise it by shielded lines, by physically separate routing or by spacers in the cable trays.
Other typical sources of interference include power electronics, switching operations (contactors) and equipotential bonding differences. The following principles apply:
There is widespread lack of awareness and attention with regard to another major cause of excessive loads on existing bonding systems (e.g. cable shielding), namely, incorrect or insufficiently dimensioned return current paths. An increasing degree of automation is accompanied by greater demands on the speed and control accuracy of the drives. Ever increasing pulse speeds and the accompanying higher frequencies have resulted in a hugely growing impact of stray capacities on the generation of higher-frequency vagrant currents (for example, in the line leading from a phase to the PE conductor). Particularly in case of asymmetric motor cables this results in an induction on the PE (Ipe) within the cables. Currents are generated that return to their source (the inverter or the motor cable itself) always following the path with the least impedance. It is not uncommon that such higher-frequency compensating currents flow through shield connections of industrial data cables or through measurement/sensor lines (running parallel to the equipotential bonding or to earth connections) resulting in malfunctions in the connected periphery.
A prerequisite to keep the above described problems under control consists in using symmetrical motor lines combined with professional expert installation of an adequate earthing and equipotential bonding system.
Do you have any questions or would you like advice from our experts? Simply send us your enquiry - conveniently online.