Indirect maintenance costs
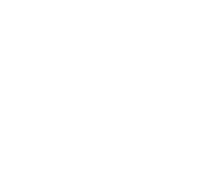
The costs of unplanned downtime are increasing significantly across nearly all industries. Compared to the last two years, the costs for one hour of unplanned downtime in production have risen by at least 50%. For example, in the automotive industry, the costs for one hour of downtime have surpassed 2 million US dollars.
The publicly available report "The True Costs of Downtime, 2023" examined the 500 largest companies worldwide. One of the findings is that in addition to the direct costs of downtime, overall losses have also increased significantly.
For an average-sized facility (in the CRITICAL FMCG sector), costs are estimated at 129 million US dollars per year. According to the report, an average production facility experiences approximately 20 instances of downtime per month, resulting in over 25 hours of unplanned downtime. This poses a significant burden on the operating results.
The increasing costs and losses due to unplanned downtime underscore the urgency for businesses to implement effective maintenance strategies to maintain their competitiveness and minimize financial losses.
Indirect maintenance costs are a crucial aspect in the maintenance industry that is often overlooked but can have significant impacts on a company's bottom line. These costs are expenses incurred during downtime but are not directly related to the repair or maintenance of equipment. In this glossary entry, we will delve deeper into what indirect maintenance costs are and how they impact the bottom line.
One of the most significant indirect maintenance costs is the cost of production outages. When machines or equipment are idle due to maintenance or failures, this leads to unused production capacity. During these downtime periods, no products can be manufactured or sold, resulting in significant revenue losses. These costs are often difficult to quantify but can have a significant impact on the bottom line.
To compensate for production outages and resume operations, overtime for personnel is often required. This leads to higher labor costs as employees must work outside their regular hours. These additional labor costs can add up and strain the budget.
During downtime, there may be quality losses. Production delays and unexpected interruptions can affect product quality. This can result in customer dissatisfaction and affect the company's brand image. In the long run, this can lead to a decline in customer loyalty and revenue loss.
The impacts of indirect maintenance costs are not limited to the company itself but can also affect customers and suppliers. Delivery delays due to production outages can lead to contract breaches or penalties. This can undermine the trust of customers and suppliers in the company and jeopardize long-term business relationships.
During downtime, it may be necessary to deploy additional labor to maintain operations or perform repairs. This can lead to increased personnel costs, as specialized or external labor may be required. Additionally, maintaining an efficient maintenance process requires regular training and development for maintenance personnel, which can incur additional costs.
To prepare for downtime, companies often need to maintain an adequate amount of spare parts and materials in inventory. This results in inventory holding costs, including warehouse rent, insurance, depreciation, and other inventory management costs. Inefficient inventory management can lead to excessive stock levels and higher costs.
Managing and coordinating maintenance activities requires time and resources from managers and administrators. This includes planning maintenance, coordinating labor, and monitoring maintenance processes. These management and administrative costs should also be included in the overall consideration of indirect maintenance costs.
Production downtime consists of planned and unplanned equipment shutdowns. Planned downtime occurs when maintenance or repair activities are planned and carried out to optimize equipment performance and prevent failures. On the other hand, unplanned downtime is of a technical nature and occurs unexpectedly due to equipment failures or malfunctions.
Experts like Heinz-Joachim Schulte estimate that approximately 20% of downtime is unplanned and technical in nature. These unplanned downtimes can have significant financial impacts.
According to the report "The True Costs of Downtime 2023" the costs of unplanned downtime for Fortune Global 500 companies now amount to approximately 11% of their annual revenue - nearly 1.5 trillion US dollars. These enormous costs underscore the urgency for companies to implement efficient maintenance strategies to minimize unplanned downtime and maintain their competitiveness.
The financial impacts of unplanned downtime on the overall economy are significant and highlight the need for effective maintenance practices. By identifying and minimizing unplanned downtimes, companies can not only reduce costs but also increase productivity and enhance their competitiveness.
These insights are based on the study "THE TRUE COST OF DOWNTIME 2023," Senseye, assessments by the renowned OEE expert Heinz-Joachim Schulte, as well as our own surveys and experiences from over 150 OT network experts at Indu-Sol GmbH.
Stay informed! Receive the latest offers and news about industrial networks and their optimization - conveniently via e-mail.