Technical emergency service
– System problems? Downtime?
Request a service technician now!
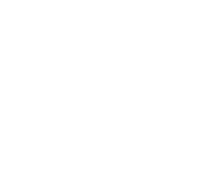
Is your system down or experiencing a production outage? In these urgent cases, our service is available to you. You can reach us 24/7 at the following telephone number:
Fast help without contract terms - we are there for you.
We would also be happy to advise you on our fee-based service contracts. With these, we guarantee you online support and predefined response times during which a technician will be on site at your premises.
If you have any questions about Indu-Sol products and solutions, please use our free telephone customer support.
In today's fast-moving industrial world, system/machine failures can have serious consequences. Costs skyrocket and the management level also comes under pressure. Indu-Sol and its measurement engineers understand this urgency and offer a specialized SOS service that is used by countless companies in a wide range of industries every year. Not only are we on site within 24 hours to fix the problem, but we also analyze the underlying systemic causes to prevent future failures. We also organize international SOS assignments with the help of our global partner network.
Indu-Sol does not only stand for emergency assistance. To ensure that our customers can operate profitably in the long term, Indu-Sol takes care of sustainable network stability and operational reliability for its customers.
Call us now +49 (0)34491 / 580-0
or fill in the form
Call us now +49 (0)34491 / 580-0
or fill in the form
Whether for PROFIBUS, PROFINET, Ethernet/IP, CAN, Industrial Ethernet, EMC and much more. Indu-Sol carries out targeted troubleshooting and diagnostics in all communication protocols commonly used in industry. The steps are described below using PROFINET troubleshooting:
Step 1: System inspection and visual inspection of the installation as far as possible with a local employee.
Step 2: We check the transmission quality of the network communication with the PROFINET-INspektor® NT (while the system is running) and evaluate all telegrams of the logical data traffic as well as events (error telegrams, telegram gaps, jitter) including any alarm messages that may occur.
Step 3: We analyze the entire network (with the system running) using the PROscan® Active V2 software and create an up-to-date topology plan. There are often more extensive network connections than known, which means that causes for increased network loads, for example, can also be suspected here. We check cable lengths, attenuation reserves and wiring changes.
We determine the temporal course of the network load distribution in the entire network by analyzing the managed switches (with the system running) using the PROmanage® NT software, i.e. port-specific allocation of the generated network load and any errors that may occur.
Step 4: We analyze the EMC environment for electromagnetic coupling and stray currents (when the system is running) with the EMCheck® ISMZ I, i.e. the shielding currents of data cables and in the equipotential bonding system. With the EMCheck® MWMZ II, we evaluate the impedance of the shields and equipotential bonding conductors, analyze the shielding effect and the signal reference.
If the analysis indicates problems in the wiring, we start a cable test. Length-dependent values for crosstalk (near-end cross(X)-talk) and insertion loss are also checked.
In maintenance, the key to avoiding unplanned system downtimes is to use a condition monitoring system. Using tools such as the PROFINET-INspektor® NT, maintenance engineers can continuously monitor network communication. This makes it possible to detect irregularities caused by wear and tear on cables, plugs and devices, for example, at an early stage. By analyzing the network communication and environmental parameters, the assets of your plant can be monitored, anomalies identified and proactive corrective measures taken in good time before they lead to failures. This approach not only leads to higher plant availability, but also optimizes the use of human resources.
Reduction of future downtimes: Our SOS service aims not only to solve acute problems, but also to identify and eliminate potential sources of faults. This leads to a significant reduction in unplanned production stops and therefore increases overall equipment effectiveness (OEE).
Increased productivity and profitability: Increasing the reliability of OT networks enables more stable production. This increases the efficiency of the systems and contributes to improved profitability.
Optimization of plant availability: The holistic Indu-Sol approach, which includes both preventive measures and rapid troubleshooting, maximizes plant availability. This supports continuous production and minimizes delays.
Increasing safety and reducing risks: Indu-Sol experts assist in minimizing risks from electromagnetic interference and network problems. This leads to a safer production environment and protects the investments made.
By using our SOS services and implementing preventive strategies such as OT network condition monitoring, companies are investing in the reliability and sustainability of their business.