Ausfallkosten
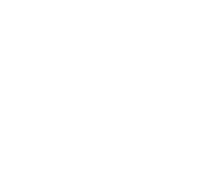
Die finanziellen Folgen von Anlagenausfallzeiten – ob geplant oder ungeplant - sollten in der Industrie nicht unterschätzt werden. Unterschiedliche Quellen berichten, dass eine Stunde ungeplanter Stillstand in der Automobilindustrie mittlerweile rund 1,85 Mio. € Dollar kostet. Auch bei den schnelldrehenden Konsumgütern (FMCG) oder in der Lebensmittelindustrie sind Ausfallkosten pro Stunde zwischen 40.000 und 200.000 € nicht unüblich. Dieser Artikel zielt darauf ab, ein tieferes Verständnis für die Berechnung sowohl greifbarer als auch immaterieller Ausfallkosten zu schaffen und gleichzeitig Strategien für Werksleiter aufzuzeigen, um diese Kosten zu minimieren und die Gesamteffizienz zu steigern.
Zu den direkten, quantifizierbaren Kosten gehören:
Bei ungeplanten Stillständen müssen oft Mitarbeiter Überstunden leisten, was zusätzliche Kosten verursacht. Überstunden werden in der Regel höher vergütet als reguläre Arbeitsstunden. Angenommen, der normale Stundenlohn beträgt 18,5 € und der Überstundensatz liegt bei 1,6x, also 29,6 € pro Stunde. Für die Reparatur der Produktionslinie über 5 Stunden durch 6 Mitarbeiter entstehen Kosten von rund 880 €.
Kosten der Leerlaufarbeitsstunde: Fallen an, wenn Mitarbeiter während eines Stillstands bezahlt werden, ohne produktiv zu sein. Diese Kosten entstehen durch die Fortzahlung der Gehälter trotz Produktionsausfall und werden durch Multiplikation der Leerlaufstunden mit den durchschnittlichen Kosten pro Stunde berechnet.
Beispiel: Bei einem Stillstand von 2,5 Stunden in einer Produktionslinie mit 25 Arbeitern, die durchschnittlich 18,5 €/Std. verdienen, entstehen Kosten für ungenutzte Arbeitskraft in Höhe von 1.156,25 € (25 Arbeiter x 18,5 €/Std. x 2,5 Stunden).
Reparaturkosten fallen an, wenn Ausfallzeiten durch technische Defekte verursacht werden. Sie umfassen Aufwendungen für Ersatzteile, den Einsatz spezialisierter Arbeitskräfte und die benötigte Ausrüstung zur Behebung des Problems und Wiederherstellung der Anlage.
Immaterielle Kosten beinhalten:
Durch strategische Planung, den Einsatz moderner Technologien und die Förderung eines proaktiven Teams können Werksleiter nicht nur die direkten und indirekten Kosten von Ausfallzeiten minimieren, sondern auch die Gesamteffizienz und Wettbewerbsfähigkeit ihres Unternehmens verbessern. Eine Investition in die Vermeidung von Ausfallzeiten ist daher nicht nur eine Absicherung gegen finanzielle Verluste, sondern auch ein Schritt hin zu einer nachhaltigeren und produktiveren Zukunft und einer optimalen Gesamtanlageneffektivität (OEE).
Die Implementierung eines Condition Monitoring & Security Management (CM&SM) Systems bietet eine Vielzahl von Vorteilen für Betreiber in der Industrie, insbesondere in den Bereichen vorausschauende Instandhaltung und Operational Technology (OT) Security. Durch die frühzeitige Erkennung von potenziellen Problemen und Sicherheitsbedrohungen können Unternehmen nicht nur Ausfallzeiten und deren Kosten minimieren, sondern auch die Lebensdauer ihrer Anlagen verlängern und die Sicherheit ihrer operativen Technologie gewährleisten. Hier sind die Kernvorteile eines solchen Systems:
1. Frühzeitige Fehlererkennung: CM&SM Systeme ermöglichen die kontinuierliche Überwachung und Analyse des Zustands von Maschinen und Anlagen. Durch die Erfassung und Auswertung von Daten wie Vibration, Temperatur und Leistung in Echtzeit können Anomalien frühzeitig erkannt werden. Dies ermöglicht präventive Wartungseingriffe, bevor es zu kostspieligen Ausfällen kommt.
2. Verbesserte Anlagenverfügbarkeit: Durch die Verringerung ungeplanter Stillstände mittels präventiver Wartungsmaßnahmen können Betreiber die Verfügbarkeit und Zuverlässigkeit ihrer Anlagen deutlich steigern. Dies führt zu einer kontinuierlichen Produktion und vermeidet Produktionsverluste.
3. Kosteneinsparungen: Die Reduzierung von Ausfallzeiten und die Vermeidung schwerwiegender Anlagenschäden durch frühzeitige Wartung führen zu erheblichen Kosteneinsparungen. Diese Einsparungen resultieren aus geringeren Reparatur- und Ersatzteilkosten sowie aus der Optimierung von Wartungsplänen, die unnötige Überprüfungen reduzieren.
4. Erhöhung der OT-Security: CM&SM Systeme tragen zur Sicherheit der Operational Technology bei, indem sie kontinuierlich den Netzwerkverkehr überwachen und auf Anomalien prüfen. Dies hilft, Cyberbedrohungen und Schwachstellen frühzeitig zu identifizieren und Gegenmaßnahmen einzuleiten, um die Integrität und Vertraulichkeit kritischer industrieller Steuerungssysteme zu schützen.
5. Datenbasierte Entscheidungsfindung: Durch die Sammlung und Analyse von Betriebsdaten ermöglichen CM&SM Systeme eine fundierte Entscheidungsfindung. Betreiber können Wartungs- und Investitionsentscheidungen basierend auf genauen Daten über den Zustand und die Leistung ihrer Anlagen treffen.
6. Verbesserte Sicherheit und Compliance: Ein weiterer wichtiger Vorteil ist die Verbesserung der Sicherheit für Mitarbeiter und die Einhaltung regulatorischer Anforderungen. Durch die Verhinderung von Unfällen und Ausfällen, die durch übersehene Anlagenprobleme verursacht werden können, tragen CM&SM Systeme dazu bei, die Arbeitsumgebung sicherer zu machen und Compliance-Standards zu erfüllen.
7. Langfristige Anlagenoptimierung: Die langfristige Sammlung und Analyse von Zustandsdaten ermöglicht eine tiefgreifende Einsicht in die Leistungs- und Verschleißmuster von Anlagen. Dies unterstützt Betreiber dabei, Optimierungsstrategien für ihre Anlagen zu entwickeln, die Lebenszykluskosten zu senken und die Gesamteffizienz zu steigern.
Insgesamt bietet die Integration eines CM&SM Systems in die Betriebsstrategie von Industrieunternehmen eine solide Grundlage für die Verbesserung der Wartungseffizienz, die Erhöhung der Anlagensicherheit und die Gewährleistung einer höheren Systemresilienz gegenüber operativen und sicherheitstechnischen Risiken.
Schlussfolgerung
Die finanziellen Auswirkungen von Ausfallzeiten sind erheblich und steigen weiter an. Experten gehen davon aus, dass die Gesamtverluste durch Ausfallzeiten für ein Industrieunternehmen bis zu 11% des Umsatzes ausmachen können. Dagegen stehen durchschnittlich rund 3% an Investitionen in das Instandhaltungs-Budget gegenüber. Wie die Zahlen belegen, sind in den Anlagen in Zukunft bei konsequenter Umsetzung einer vorausschauenden Instandhaltungsstrategie noch deutliche Gewinnpotenziale zu heben.
Bleiben Sie informiert! Erhalten Sie Angebote und Neuigkeiten rund um industrielle Netzwerke sowie deren Optimierung – bequem per E-Mail.