Indirekte Instandhaltungskosten
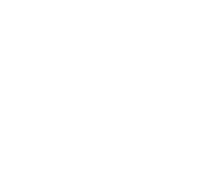
Die Kosten für ungeplante Ausfallzeiten steigen in nahezu allen Branchen signifikant. Gegenüber den letzten zwei Jahren sind die Kosten für eine Stunde ungeplanter Ausfallzeit in der Produktion um mindestens 50% gestiegen. In der Automobilindustrie beispielsweise sind demzufolge, die Kosten für eine Stunde Ausfallzeit auf über 2 Millionen US-Dollar gestiegen.
Der öffentlich zugängliche Bericht „The true costs of downtime, 2023*“ hat die 500 größten Unternehmen weltweit unter die Lupe genommen. Eine der Erkenntnisse ist: Neben den direkten Kosten einer Ausfallzeit sind auch die Gesamtverluste deutlich gestiegen.
Für eine durchschnittlich große Anlage (Bereich KRITIS – FMCG) werden die Kosten auf 129 Millionen US-Dollar pro Jahr geschätzt. Ein durchschnittliches Produktionswerk hat laut Bericht monatlich ca. 20 Ausfallzeiten, und verliert dabei über 25 Stunden pro Monat durch ungeplante Ausfallzeiten. Das ist eine enorme Belastung des Betriebsergebnisses.
Die steigenden Kosten und Verluste durch ungeplante Ausfallzeiten verdeutlichen die Dringlichkeit für Unternehmen, effektive Instandhaltungsstrategien zu implementieren, um ihre Wettbewerbsfähigkeit zu erhalten und finanzielle Verluste zu minimieren.
Indirekte Instandhaltungskosten sind ein entscheidender Aspekt in der Instandhaltungsbranche, der oft übersehen wird, aber erhebliche Auswirkungen auf das Betriebsergebnis eines Unternehmens haben kann. Diese Kosten sind Ausgaben, die während Ausfallzeiten anfallen, jedoch nicht unmittelbar mit der Reparatur oder Wartung von Anlagen zusammenhängen. In diesem Glossarbeitrag werden wir genauer darauf eingehen, was indirekte Instandhaltungskosten sind und wie sie sich auf das Betriebsergebnis auswirken.
Eine der bedeutendsten indirekten Instandhaltungskosten sind die Kosten für Produktionsausfälle. Wenn Maschinen oder Anlagen aufgrund von Wartungsarbeiten oder Ausfällen stillstehen, führt dies zu ungenutzten Produktionskapazitäten. Während dieser Ausfallzeiten können keine Produkte hergestellt oder verkauft werden, was zu erheblichen Einnahmeverlusten führt. Diese Kosten sind oft schwer quantifizierbar, können jedoch einen erheblichen Einfluss auf das Betriebsergebnis haben.
Um Produktionsausfälle auszugleichen und den Betrieb wieder aufzunehmen, sind häufig Überstunden für das Personal erforderlich. Dies führt zu höheren Lohnkosten, da die Mitarbeiter außerhalb ihrer regulären Arbeitszeit arbeiten müssen. Diese zusätzlichen Lohnkosten können sich summieren und das Budget belasten.
Während Ausfallzeiten kann es zu Qualitätsverlusten kommen. Produktionsverzögerungen und unerwartete Unterbrechungen können die Produktqualität beeinträchtigen. Dies kann Kundenunzufriedenheit zur Folge haben und das Markenimage des Unternehmens beeinflussen. Langfristig kann dies zu einem Rückgang der Kundenbindung und Umsatzeinbußen führen.
Die Auswirkungen von indirekten Instandhaltungskosten beschränken sich nicht nur auf das Unternehmen selbst, sondern können sich auch auf Kunden und Lieferanten erstrecken. Lieferverzögerungen aufgrund von Produktionsausfällen können zu Vertragsbrüchen oder Vertragsstrafen führen. Dies kann das Vertrauen von Kunden und Lieferanten in das Unternehmen erschüttern und langfristige Geschäftsbeziehungen gefährden.
Während Ausfallzeiten kann es notwendig sein, zusätzliche Arbeitskräfte einzusetzen, um den Betrieb aufrechtzuerhalten oder um Reparaturen durchzuführen. Dies kann zu erhöhten Personalkosten führen, da möglicherweise spezialisierte oder externe Arbeitskräfte benötigt werden. Darüber hinaus erfordert die Aufrechterhaltung eines effizienten Instandhaltungsprozesses regelmäßige Schulungen und Weiterbildungsmaßnahmen für das Instandhaltungspersonal, was zusätzliche Kosten verursachen kann.
Um auf Ausfallzeiten vorbereitet zu sein, müssen Unternehmen oft eine ausreichende Menge an Ersatzteilen und Materialien auf Lager halten. Dies führt zu Lagerhaltungskosten, die Lagermiete, Versicherung, Abschreibungen und andere Lagerverwaltungskosten umfassen. Eine ineffiziente Lagerhaltung kann zu übermäßigen Beständen und damit zu höheren Kosten führen.
Die Verwaltung und Koordination von Instandhaltungsaktivitäten erfordert Zeit und Ressourcen von Managern und Administratoren. Dies umfasst die Planung von Wartungsarbeiten, die Koordination von Arbeitskräften und die Überwachung von Instandhaltungsprozessen. Diese Management- und administrativen Kosten sollten ebenfalls in die Gesamtbetrachtung der indirekten Instandhaltungskosten einbezogen werden.
Produktionsstillstände setzen sich aus geplanten und ungeplanten Anlagenstillständen zusammen. Geplante Stillstände treten auf, wenn Wartungsarbeiten oder Instandhaltungsmaßnahmen geplant und durchgeführt werden, um die Anlagenleistung zu optimieren und Ausfälle zu vermeiden. Auf der anderen Seite sind ungeplante Stillstände technischer Natur und treten unerwartet aufgrund von Maschinenausfällen oder Störungen auf. Experten wie Heinz-Joachim Schulte schätzen, dass etwa 20 % der Stillstände ungeplant und technischer Natur sind. Diese ungeplanten Ausfallzeiten können erhebliche finanzielle Auswirkungen haben.
Laut dem Bericht "The True Costs of Downtime 2023" belaufen sich die Kosten ungeplanter Ausfallzeiten für Fortune Global 500-Unternehmen mittlerweile auf etwa 11 % ihres Jahresumsatzes - fast 1,5 Billionen US-Dollar. Diese enormen Kosten verdeutlichen die Dringlichkeit für Unternehmen, effiziente Instandhaltungsstrategien zu implementieren, um ungeplante Stillstände zu minimieren und ihre Wettbewerbsfähigkeit zu erhalten.
Die finanziellen Auswirkungen von ungeplanten Ausfallzeiten auf die gesamte Wirtschaft sind erheblich und verdeutlichen die Notwendigkeit effektiver Instandhaltungspraktiken. Durch die Identifizierung und Minimierung von ungeplanten Stillständen können Unternehmen nicht nur Kosten reduzieren, sondern auch ihre Produktivität steigern und ihre Wettbewerbsfähigkeit verbessern.
Diese Informationen basieren auf der Studie "THE TRUE COST OF DOWNTIME 2023", Senseye, den Einschätzungen des renommierten OEE-Experten Heinz-Joachim Schulte sowie eigenen Erhebungen und Erfahrungen der mehr als 150 OT-Netzwerkexperten der Indu-Sol GmbH.
Bleiben Sie informiert! Erhalten Sie Angebote und Neuigkeiten rund um industrielle Netzwerke sowie deren Optimierung – bequem per E-Mail.